An introduction to Mokume Gane
- Owain Houghton
- Oct 12, 2022
- 5 min read
Updated: Oct 21, 2022
Mokume Gane is a name for a Japanese metal-working technique developed some 250–300 years ago. The name refers to the visual appearance, translating as wood grain metal. Three or more sheets of non-ferrous metal (not iron-based) are laminated together without the use of solder, reduced, carved, and then forged to produce patterns that often resemble wood grain.
The technique is thought to develop from decorative metalwork, notably swords, in Feudal Japan. It is widely attributed to metalsmith Denbei Shoami. The method was long-forgotten in the "west" but has seen a recent revival in the late 20th century.

Making Mokume Gane (Traditional Method)
Preparation
To make mokume gane, by any method, we must first make a billet. This involves layering sheets of the various metals. The sheets must be well-prepared to make sure they are clean. Any surface oxides, dirt, or defects (surface roughness, etc.) will be trapped in the interface once the billet is made and weaken the material.
Traditionally, sheets had to be forged from cast ingots and then worked by hand with files, scrapers, and abrasive stones to develop the smoothest, flattest surfaces possible on both sides of each sheet.
Firing and Forging the billet
Traditionally, the sheets are stacked between two iron plates that are bound with heavy iron wire, and folded iron sheets are used to hold the stack together during firing.
Firing the mokume game billet was performed in charcoal–fired forge (a hodo). Charcoal not only acts as a fuel source, but it also generates a reducing environment; this prevents the oxidation of the metal since charcoal (carbon) preferentially reacts with any oxygen.
The billet was then carefully heated to a uniform temperature. The temperature should be low enough to fuse the metal but not melt it. This is a traditional method is a form of transient-phase liquid bonding (see below). Empirically, the temperature is sufficient when the visible edges of the billet will exhibit a shine or flash. The billet is then removed and hammered on an anvil to ensure the bond is tight.
Patterning the billet
Once bonded, the billet needs to be forged down to a suitable size for the desired object:
The first step involves reducing the billet to a thinner, more useful shape. Traditionally this was done by hand. In most cases, a fault in the billet here requires scrapping!
The billet came then be carefully carved (with small chisels) and forged (flattening) to produce patterns that will slowly emerge as the process is carried out.
Finally, the worked billet can be carefully cut, shaped, and finished to produce Mokume Gane objects. While many artists continue to produce wood-grain effects or patterns, the endless combination of twisting, forging, and carving leads to unlimited possibilities.
For the manufacture of rings, the stock is rolled to the square wire, which is then can be twisted (or not!), carved (or not!), and then forged and rolled to the proper width and thickness for ring making. Alternately, rings can be made from flat sheets in the traditional soldering method or made from washers created from a flat sheet and converted to a ring using a series of dies and punches. Deep drawing mokume gane patterned sheet or un-patterned is also possible, with subsequent steps to pattern and finish the ring. A laborious but worthwhile process!
Making Mokume Gane (Modern Method)
While the essence of Mokume Gane manufacture remains unchanged, there are still a few useful developments to the modern methods:
Nowadays, commercially produced billets, plate forging rod and sheet is available for those not desiring the loss that accompanies making proper mokume gane (approximately 50%). This gives the aspiring artist materials to work with without the extra steps of creating the bonds.
It is more common to bolt together the plates of steel and a torque plate to clamp the stack for firing.
Gas-fired and electric kilns are used to better control the heat. A reducing atmosphere is still necessary. This is often achieved by packing charcoal around the billet and wrapping in foil.
Hydraulic presses have become a common choice for forging billet and the final objects. Pressing can be done either hot or cold.
Tools like rotary files called burs or drills are more often used to carve patterns today.
Metal Choice – Colorful and malleable
The choice of metal is careful. A craftsman selects the metal based on various characteristics:
Color – not just the natural bulk color but also the various patinas that can be developed through treatment. The number and thickness of layers are also important to the overall design look.
Malleability – how easily the metal can be shaped without fracture. Ideally, two metals should be processable similarly, so they work well together in a billet.
Hardness – Best results are often achieved when alloys of similar hardness are put together.
Chemical compatibility. At the interface, a mixed composition will form. We want to avoid the formation of intermetallic and other compounds that make the billet brittle and may cause the interface to fracture.
A wide range of metals and alloys can be used, including copper, gold, steel, palladium, platinum, and silver. Some favored combinations are given below:
18K Yellow Gold | Sterling Silver | |
14K Palladium-white Gold | Sterling Silver | |
14K Red Gold | Sterling Silver | |
Palladium 500 or 950 | Sterling Silver | |
18K Yellow Gold | 14K Palladium-white Gold | Sterling Silver |
14K Red Gold | 14K Palladium-white Gold | Sterling Silver |
Palladium 950 | 14K Palladium-white Gold | Sterling Silver |
Science of joining #1 – Solid-State Diffusion Bonding
Modern techniques typically use solid-state diffusion bonding, which is used for joining unlike materials together in a wide range of industries. This differs from the traditional technique, which is similar to liquid-phase diffusion bonding.

Traditionally, the stack is heated to the point at which some or all of the alloys are above their solidus temperature (begin to melt). The liquid fuses the layers together and solidifies upon cooling. Careful heat control and skilled forging are necessary.
Solid-state diffusion bonding can occur when the stack is held at a temperature just below where either metal would melt or any liquid phase would form. Atoms in one metal can move into the other metal and vice versa. Doing so is energetically favorable. Although slowly, the inter-diffusion forms a metallic bond between the layers.
Science of joining #2 – Liquid-Phase Diffusion Bonding
Liquid-phase diffusion bonding produces a billet with high strength that can be manipulated greater without the risk of delamination and with fewer necessary annealing steps during working compared to solid-state diffusion bonding. Furthermore, liquid-phase diffusion bonding occurs over a far shorter time period.
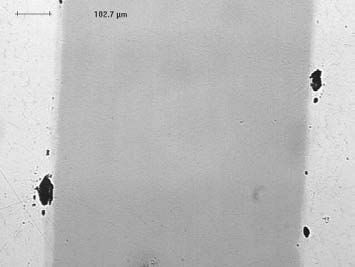
Liquid-phase diffusion bonding occurs, as the name suggests, with the interface in a liquid state rather than a solid state:
Diffusion can occur similarly to solid-state diffusion bonding when the metal is heated.
This leads to a change in composition near the interface of the two metals, and so we are likely to form a composition with a lower melting point (closer to the eutectic point).
The metal (of new composition) at the interface will melt with continued heating. At the liquidus temperature, the liquid phase flows and helps fill any voids and gaps at the interface. On cooling, the interface solidifies, forming a strong bond.
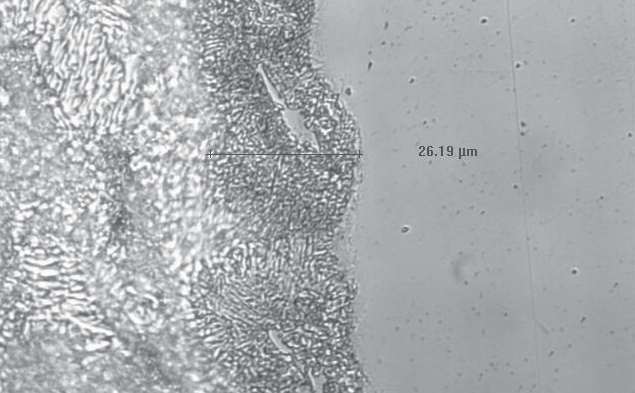
Compared with solid-state diffusion bonding, this process occurs at higher temperatures for shorter time periods. It's practical applications are discussed below.
Want more?
Read more about Mokume Gane, written by James Binnion, Chris Proof, Stewart Grice, and others:
For a how-to guide for small manufacture:
For modern techniques discussing Mokume Gane via solid or liquid-phase diffusion bonding:
We thank Chris Ploof for his support in writing this article.
Comments