Common casting defects: what causes them?
- Owain Houghton
- Sep 30, 2022
- 3 min read
Updated: Oct 22, 2022
Casting is the process of solidifying molten metal in a mold to achieve a particular semi-finished shape or to produce ingots, etc., for further working.
As seen in "what happens to a metal during casting," the casting process should be carefully controlled to control the microstructure, notably grain size. There are still many other common issues that can occur during casting, which metallurgists can explain.
Segregation and coring
When a metal alloy solidifies, it usually solidifies as dendrites. This is due to an effect called constitutional undercooling, which is not necessary to explain. Essentially, as seen from the phase diagram, the composition of the liquid and solid in the "mushy zone" during solidification are not the same. Some of the "solute" in the solid is rejected into the liquid.
As solidification proceeds, more solid forms from a progressively more "solute-rich" liquid. Hence the composition of the solid changes. This is known as "coring". As seen in the phase diagram, if an alloy has an overall composition of X, when molten, it has a uniform composition. At a given temperature T, where T lies in the "mushy zone", the liquid will have composition P, and the solid will have composition Q. As the temperature drops to T, the solid now forming approaches composition X, while the remaining liquid has composition R (due to the deficit of solute in the solid that first formed).

Due to this partitioning effect of solute between the liquid and solid, the composition of the final liquid to solidify can be very different composition to the main solid. This leads to the segregation of solutes at grain boundaries.
Segregation creates many issues regarding corrosion resistance and mechanical properties – while small grain size increases strength (Hall-Petch Relation), the grain boundaries themselves are sites of weakness. The structure is often refined and homogenized (made uniform) through working and annealing to alleviate these concerns.
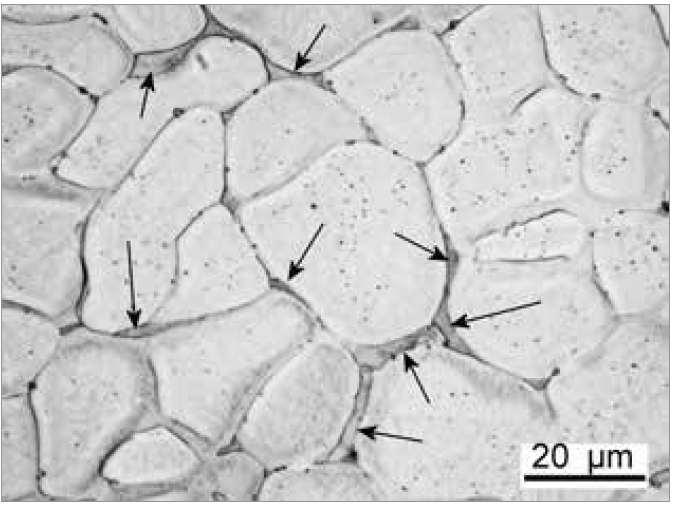
Porosity
Water and ice have different densities. Ice is a famous but peculiar exception because the solid is less dense than the liquid. In most cases, the solid is denser than the liquid. For a given amount of molten metal will shrink upon solidification. The atoms in a solid are more densely packed in the ordered crystalline lattice compared to the random arrangement in a liquid.
When casting, the mold is a fixed volume, and so is the solidification upon shrinkage (typically 5% for gold alloys). This discontinuous "jump" in density makes crystallization a "first-order" transformation.
In large ingot castings, a shrinkage cavity can form on top of an ingot or casting. To avoid this, it may be necessary to provide a reservoir of molten metal to allow for this shrinkage.
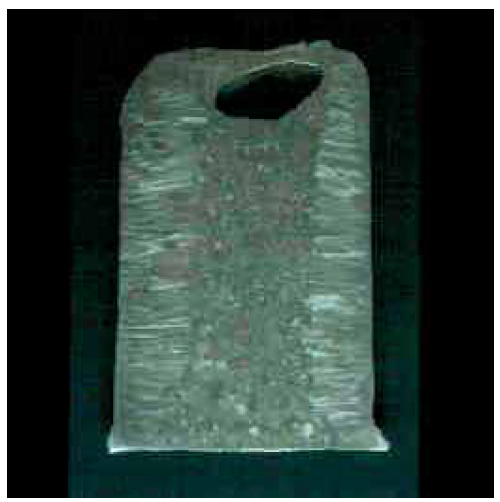
Sometimes the top of the casting can solidify prematurely, leaving molten metal inside, which will also shrink on solidification, leading to internal porosity or a “pipe,” as it is known (see above).
Small-scale internal porosity?
Smaller-scale internal porosity can arise from shrinkage, too. When dendrites form, the "arms" of the dendrites have a small space between them. Even if the liquid is fluid enough to fill those gaps, the final solidification shrinkage may lead to small porosity, especially if the insufficient molten metal is fed back into this region during casting.
Internal shrinkage porosity is typically difficult to avoid for investment casting, especially for alloys with a wide solidification range or castings with complicated shapes (where feeding metal is difficult). Such shrinkage porosity leads to a dramatic reduction in strength – the pores act as starting points for cracks.

In this example of shrinkage porosity, the spacing between dendrite arms is clear to see.
Alligatoring in ingots
If a metal casting temperature is relatively high, and thereby the cooling rate in the mold is high, then the microstructure of an ingot will typically show columnar growth to the center.
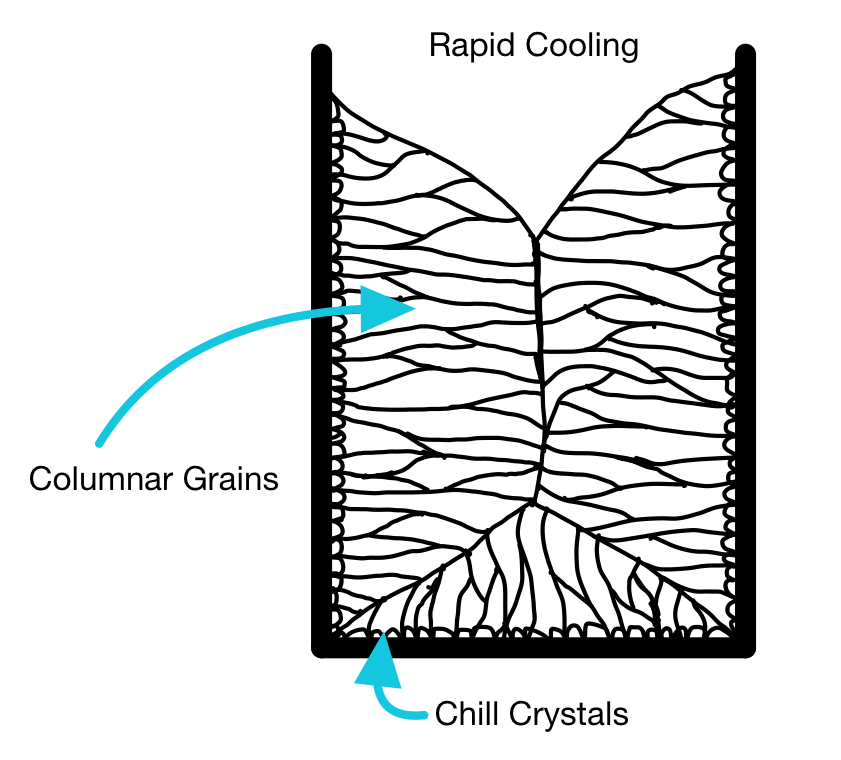
The columnar growth leads to a continuous "seam" in the center of the casting. This "seam" is essentially a series of grain boundaries. Grain boundaries are a major point of weakness; they are points along which cracks can easily propagate (like mortar in a wall of bricks).
This is not a good structure if you are going to roll the ingot to a plate or sheet, as it may split down the middle (known as alligatoring).
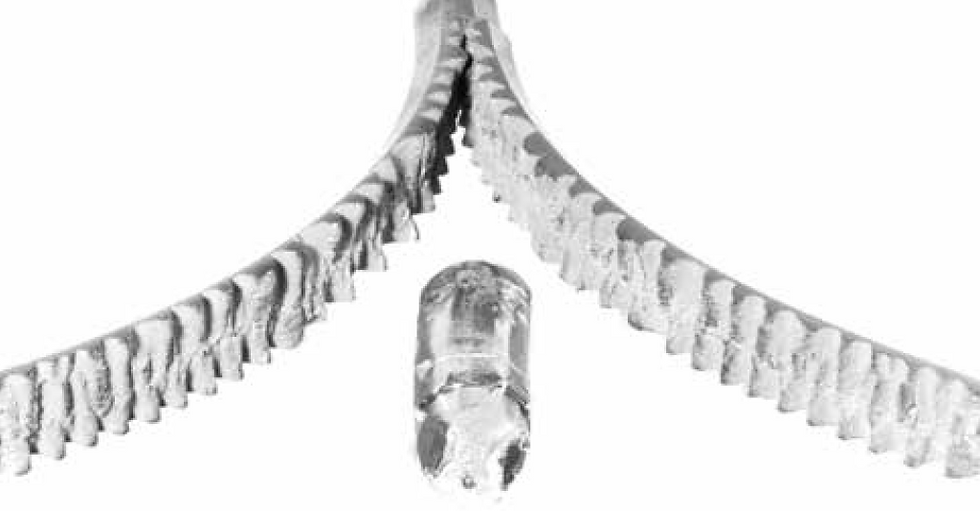
Коментарі