An introduction to soldering
- Owain Houghton
- Oct 11, 2022
- 4 min read
Soldering involves joining two pieces of metal by melting and solidifying a filler material between them. In soldering, the pieces being joined do not melt (only the filler metal, the solder, is melted). Strictly speaking, this process should be called Brazing since it tends to be carried out above 450˚C (840˚F), the arbitrary temperature separating brazing from soldering.
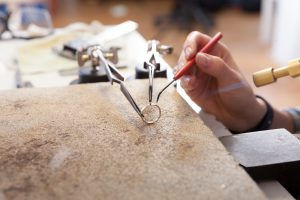
Soldering Technique
To make good soldered joints, we rely on capillary forces to encourage the flow of molten solder along the joint gap, so a thin joint gap is preferred. Thin joint gaps also give rise to stronger joints.
For good soldering:
Focus the heat on the parent metal, and allow the solder to melt and flow along the gap, preferably towards the hotter end.
We need clean, oxide-free surfaces to ensure good wetting of the solder over the to-be-soldered surfaces. Solder fluxes appropriate to the soldering temperature are recommended.

Choosing the correct solder
For jewelry materials, the solder chosen should have the following properties:
The solder should have a lower melting range than that of the parent metals being joined. As a general rule, the liquidus temperature of the solder should be ≥25˚C/45˚F below the solidus temperature (where the alloy begins to melt) of the parent alloy.
The solder melting range (the difference between the liquidus and solidus temperatures) should be suitable. Many solders are often based on eutectic compositions (i.e., they have a low melting range).
The molten solder should have good fluidity to enable it to flow into the joint gap.
The color should match the parent metal as closely as possible, so no solder lines are visible. This is not always easy to achieve, especially for high-karat or high-copper gold alloys.
The fineness/karatage should match the parent metals where possible but should certainly conform to hallmarking/stamping regulations where lower fineness/karatage solders may be allowed.
The solder should be chemically and metallurgically stable, and compatible with the parent metal. One does not want brittle phases to form in the joint area or for the solder to tarnish in service preferentially.
The soldered joint should have reasonable properties (e.g., strength, ductility, wear and tarnish resistance) compatible with the parent metals being joined.
Solder alloys should preferably be relatively easy to cast and work to the desired form, but some solders are often hard and difficult to work.
Their incorporation in recycled scrap should not lead to later problems such as embrittlement, as is the case for lead-tin-based solders.
Solders should be free of toxic elements, notably Cadmium. Although widely used in some parts of the world, a full range of cadmium-free solders are available, up to 22K.
As a result of these requirements into account, it is perhaps not so surprising that many solders are based on the parent alloys in composition but with alloying additions to lower their melting range. Typically:
Colored karat-gold solders are typically based on gold-copper-silver alloys, often close to eutectic compositions, because they have the lowest melting temperatures.
Platinum and Palladium have no real color-match problems – they may be platinum, palladium-based, or white-gold alloys.
As with gold, solders are based on parent silver alloys with alloying additions to lower melting ranges for the silvers.
The selection and evaluation of various solders have been discussed by Grice.
Solder is often used as wire or small coupons (paillons) cut from strip. In some cases, other forms may be more useful:
For items produced by stamping, a solder-flush strip or sheet (where a layer of solder is bonded to the sheet) is often used for one-half of the jewelry; the two matching halves are then jigged together and passed through a belt furnace to effect the soldering.
For chain making, the use of solder-cored wire makes post-soldering easier than the traditional solder powder method, although in situ laser welding is now finding favor.
Step-wise soldering and Solder Grades
In many cases, a series of solders with a range of melting temperatures enable step soldering in fabrication and safe soldering in repair situations. Starting with a higher melting point solder and progressively working downward permits the soldering of a number of joints in close proximity with little risk of previous joints being re-melted.
This gives rise to the terms hard (highest melting point), medium, easy and extra easy, for example, to describe such solder grades. Sadly, solder manufacturers have no uniformity in applying these descriptions. A medium karat-gold solder from one manufacturer may have a similar or lower melting temperature to one from another manufacturer described as easy.
Soldering Fluxes – A guide
Conventional fluxes are based on borax (sodium tetraborate) with other additions such as boric acid and silicofluorides, usually made with potassium salts rather than sodium to prevent the yellow glare. Such fluxes remove surface oxides and contaminants by the dissolution of the oxides before the solder melts and then by excluding oxygen ingress to prevent further oxidation during solder flow.
Ceramix-based fluxes are a more recent development that can be easily removed with hot water and brushing after soldering. If left on the jewelry, they may lead to localized corrosion.
Should I use Solder paste?
Solder paste has many advantages over conventional solder paillons to make joints. Solder pastes are simply normal precious metal solders in powder form, mixed with an organic binder to make a paste, which volatilizes off to leave no residue. Often, for torch soldering in air, they will also contain some appropriate flux. The fluxless version is usually used for belt furnace soldering under a protective atmosphere.
They can save a bench worker a great deal of time since positioning is less critical, and so productivity is far higher. It is also easier to control the amount of solder used. However, solder pastes are more expensive and have a shorter shelf-life.
Solder pastes can be purchased in all the usual colors (for gold), a full range of compositions (i.e., easy, medium, hard grades, etc.) in the full range of karats/finenesses. Solder pastes are available for gold, silver, platinum, and palladium jewelry. They are usually purchased ready for use in plastic syringes of various sizes (weights) and needle/nozzle sizes.
Comments