The science of strengthening metals
- Owain Houghton
- Jul 28, 2022
- 4 min read
Updated: Oct 21, 2022
Increasing the strength and hardness (i.e., scratch resistance) is one of the main areas of research for precious metal metallurgists. Many new technologies are on the horizon, but the widely used fundamental strengthening mechanisms are explained below.
A reminder of how metals deform
Metals are polycrystalline. In a crystal, atoms are arranged in a pattern that repeats in all three dimensions. The material is made up of many small crystals; these crystals will have the same structure and composition but are oriented differently. They are known as grains. Because of their different orientation, the grains do not pack perfectly, and the regions that separate them are known as grain boundaries.
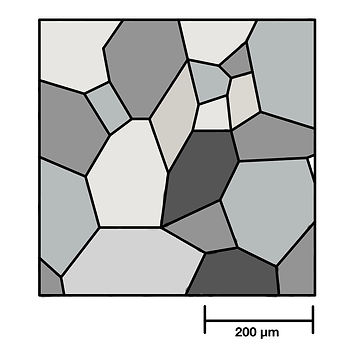
Plastic (irreversible) deformation occurs by layers of atoms sliding over one another. This is known as "slip". Slip leads to a change in the shape and orientation of grains in the microstructure and, ultimately, a change in the shape of the material.
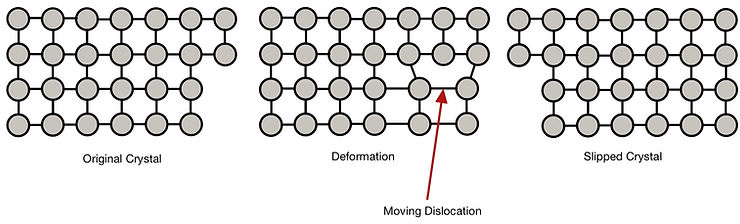
A type of crystal defect known as a dislocation is necessary for slip to occur. These types of defects are specific to each crystal. Strengthening mechanisms work by hindering (resisting) the dislocations' motion, so a larger force (stress) is needed for slip to occur.
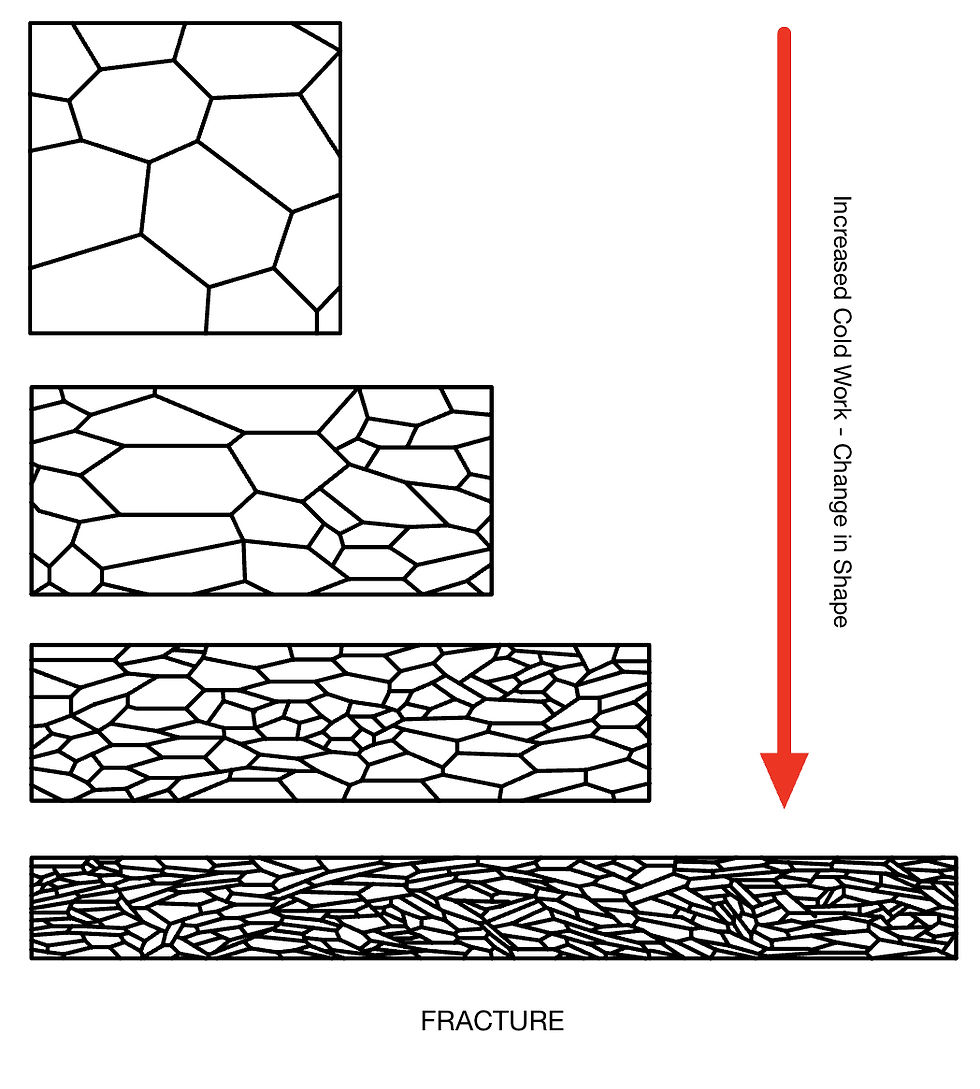
When a force is applied to a metallic object and irreversibly changes shape, it deforms plastically. The layers of atoms in the crystal slide over one another in a mechanism known as 'slip'. This results in a change in the shape and orientation of each grain and an overall macroscopic shape change.
Types of Strengthening mechanisms
The main forms of strengthening mechanisms for jewelry materials are as follows:
Processing: Grain-size control
Processing: Cold Working
Alloying: Solid solution strengthening
Alloying: Two-phase microstructures
Alloying and Processing: Precipitate Hardening
Grain-size control
When a polycrystalline material deforms, each grain must be deformed. The change in the shape and orientation of grains must be consistent with neighboring grains. This means multiple slip events are required, and so a larger force.
The smaller the grain size, the larger the strengthening eggiest. This is expressed by the Hall-Petch relationship. Yield strength is inversely related to the grain size required. Thus the jewelry is stronger and harder if it is fine-grained and beneficially; it is also more ductile and less prone to cracking, impurity embrittlement, and the “orange peel” surface after deformation.
Cold Working
As we work a material, there is a change in microstructure. Namely a reduction in grain size, shape, and orientation. This leads to an increase in the number of defects (incl. grain boundaries). These defects hinder the motion of dislocations and therefore hinder further deformation. This is known as work hardening.
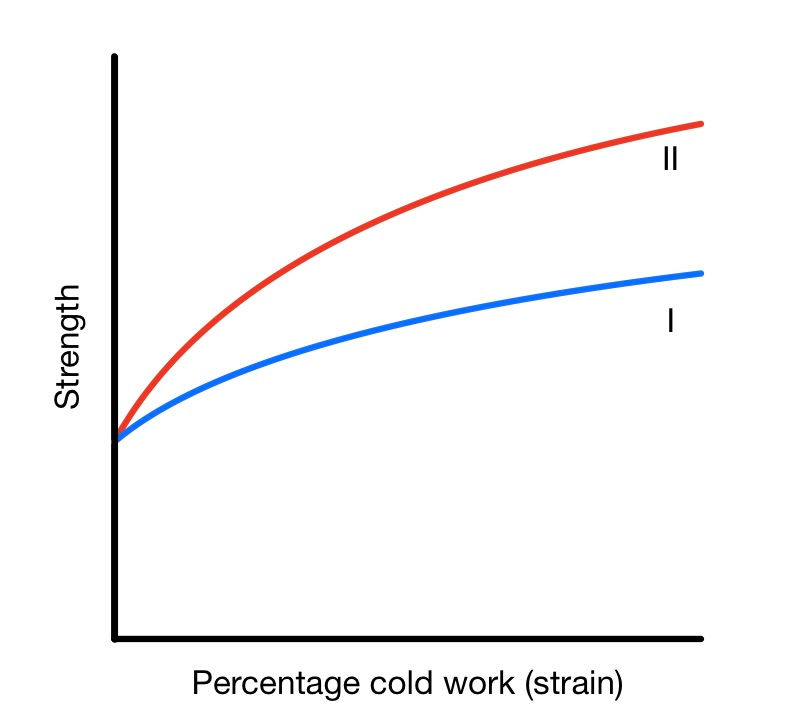
The extent of cold working depends on the alloy. Some alloys are easier to work harden than others. This depends on their composition, as well as other factors. For example. Gold-Copper alloys work harden more than Gold-Silver ones.
Two-phase microstructures
The general presence of a second phase, with a similar volume fraction to the primary phase, helps to generate a strengthening effect. This provides a mild strengthening effect as the different phases will deform differently and so hinder one another.
Solid-solution Strengthening
When an alloy exists as a single phase, it typically forms a "solid solution". The added element will occupy a random position in the crystal lattice. In most precious metal alloys, the added element will substitute for another atom in the crystal lattice. If the element differs in size, then the lattice will become strained and distorted.

The strain induced by the substitutional atom makes it more difficult for the layers of atoms to move. A larger size mismatch means a stronger strengthening effect. This is known as "solid-solution" strengthening.
Why is copper better at strengthening gold alloys than silver?
Alloying gold with copper leads to a stronger strengthening effect compared to silver because there is a greater size mismatch (see table below). This means the lattice is distorted more, and so the layers of atoms in the crystal have much more difficulty sliding over one another.
Metal | Crystal Structure | Density (g/cc) | Melting Point (˚C) | Relative Size |
Gold | FCC | 19 | 1064 | 1.00 |
Silver | FCC | 11 | 962 | 1.07 |
Copper | FCC | 9 | 1085 | 1.12 |
Platinum | FCC | 21 | 1772 | 0.96 |
Palladium | FCC | 12 | 1552 | 0.95 |
Cobalt | FCC | 9 | 1495 | 0.88 |
Zinc | HCP | 7 | 419 | 0.98 |
Nickel | FCC | 9 | 1453 | 0.86 |
Iridium | FCC | 23 | 2410 | 0.94 |
Ruthenium | HCP | 12 | 2334 | 0.93 |
Tin | Tetragonal | 7 | 232 | 1.01 |
Precipitate Hardening
If the element has a dissimilar size, very different chemistry, or we add too much of it, then it may be energetically favorable to form a second phase. This phase may have either a different composition, crystal structure, or both.
Precipitation is where a second phase (with a different composition) forms within another. In a solid, these precipitates tend to form preferentially at grain boundaries. Adding a second phase with a different crystal structure makes it difficult for these dislocations to move. As a result, the material is more resistant to deformation.

When we anneal the alloy to restore ductility, the metal has a single-phase microstructure. The alloy is then quenched (cooled quickly in water), so the microstructure is "frozen-in". At high temperatures, the atoms have the energy to rearrange themselves. By cooling quickly, they don't have sufficient time to diffuse (move) around and form second phases.
The alloy is then aged (heated) at a high temperature within the two-phase field of the phase diagram. This allows precipitates to grow and coarsen. The size and distribution of these precipitates dramatically affects their strengthening effect; it must be carefully controlled during working and annealing (processing).
Achieving the optimum or "peak" hardening is a function of temperature and time. As we anneal for longer, the precipitates grow larger.

When the precipitates are small, they provide little resistance to deformation. The precipitates can be easily deformed or "cut". When the precipitates are too large (coarse). The precipitates do not interact strongly with dislocations, and so the strengthening effect is very weak.
There is a fixed amount of solute that can form precipitates. As a result, as the precipitates get larger, there are fewer of them. The best distribution is achieved when there is a distribution of many small precipitates – a fine microstructure.
Summary table
Strengthening Mechanism | Strength of effect | Necessary material properties |
Cold Working | Moderate | Any crystalline metal |
Grain-Size Control | Moderate | Any crystalline metal |
Two-phase microstructures | Moderate–High | A two-phase crystalline metal |
Solid Solution Strengthening | Moderate – High | An alloy phase with high solubility of other elements |
Precipitate Hardening | High | Two-phase alloy formed by ageing the single-phase. |
Comentários