Welding in Jewelry
- Owain Houghton
- Oct 15, 2022
- 2 min read
Updated: Oct 21, 2022
Welding involves joining two pieces of metal together by melting them with or without filler material. The pieces being joined must be in good contact and heated locally to melt the joint surfaces together. The metal will then solidify, forming a metallic bond between the two parts.
Microstructure of a weld
The microstructure of a weld has some key features:
The melted metal will solidify a classic dendritic-cast microstructure
Around the weld is a heat-affected zone (HAZ) which absorbs heat from the molten metal during solidification.
The size (width) of the weld zone will depend on the heat source used and the properties (conductivity) of the weld materials. A large gas torch, for example, will produce a larger (wider) weld zone than a laser, where the heat energy can be finely focused and is more intense.
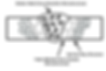
Properties of the Heat-Affected Zone
The area around the weld will not be melted but heated to a high temperature. As a result, we may see a great deal of grain coarsening and potentially the transformation into meta-stable high-temperature phases.
Grain coarsening will ultimately lead to a softer, less hard area
Meta-stable phases are typically brittle.
So a weld zone may have mechanical and corrosion properties that differ from the normal parent metal unaffected by the welding. We may also expect some surface quality degradation due to melt turbulence and oxidation, possibly with some porosity due to expelled gases.
Types of Welding
Tungsten Inert Gas (TIG) and electrical resistance spot welding use electric current to generate heat:
TIG welding – the current strike an arc between the tungsten electrode and the workpiece.
Plasma arc welding – A plasma is formed from the ionized gas surrounding the electrode, generating considerable heat.
Laser Welding – Heating can also be accomplished by an electron beam or by a laser beam.
Why is Laser Welding so popular?
Laser welding has become very common in the jewelry industry. This high-energy source allows very fine and deep welds. This means:
Repairs can be made close to set gemstones without damaging them (no removal necessary) due to a small heat-affected zone.
It is quick and precise.
It can be done in the air (no special atmosphere or flux is necessary), and there is little fixturing required.
Several welding operations can be done on the same workpiece without fear of re-melting earlier joints.
Filler metals can be used if desired, for example, in filling open porosity; these are normally of the same alloy as the workpiece, thus giving no problems with color matching or karatage mismatch.
It is particularly suitable for pure precious metals (e.g., 24-karat gold).
Laser welds tend to be stronger and more ductile than soldered joints, with little porosity. There are no toxicity problems as are associated with cadmium in solders. On the other hand, laser welding can be more time-consuming than soldering, and the welds may have a bulbous overlap surface that will need grinding and polishing. As stated earlier, it is also a line-of-sight method.
Laser welding is often used for decoration by granulation and is commonly used for making chain links in situ.